How we cast your jewellery
So, you had this great idea for a piece of jewellery, a bit of model engineering, a bagpipe key and all the rest. So where do you go from there? These are often the key starting points we begin with casting your ideas:
Preparing the Metal
We only buy our metal from the most reputable bullion dealers. Then we know that the alloy is spot on. It comes to us, supplied in grain form. All our sprues are recycled in-house and made back into clean grain. This is mixed with new bullion which gives us first class results with minimal wastage. This is done with all our metals. Cleanliness is key - we barrel polish all of our grain before casting.
Weighing out the Metal
So, how much metal do we put in each flask? We do a separate melt for each flask so we need to know the amount of metal needed accurately. By dint of weighing the waxes and a bit of Excel skullduggery we calculate the weight of metal , like using the calculator on our site. Before we start casting we have a tub of metal numbered, for each flask.
Melting and Pouring the Metal
We melt all of our metal in a Closed casting machine. This covers the metal with inert gas (nitrogen) to keep all of the oxygen away. The metal is heated in an induction furnace and when the metal reaches the required temperature, it's dropped into the flask with an extra shove of extra pressure nitrogen gas. We leave it for a couple of minutes to freeze then removed from the machine to cool in the air.
Quenching and Cleaning the Castings
When the metal reaches "black heat" the flask is plunged into a tank of cold water and swished around until all the boiling stops. By this point, most of the plaster is deposited in the bottom of the tank. The flask and castings are moved to an enclosed pressure washer where they are carefully blasted clear of plaster. A swift 5 minutes in some weak acid to soften any oxides - a good wash and into the workshop for...
Pin Polishing
The individual castings are snipped off the central core (tree trunk) and placed in a magnetic pin polisher which gives them a nice, bright, shiny finish. Ready for sprue removal, inspection and dispatch.
Our approach to quality jewellery making
From enquiry through to delivery, we've got you covered
Quality control
This key part of our process ensures our customers receive the best products.
Reliable manufacturing
Our team and supplier relationships are built on years of trust and successful business.
Same day casting
We offer fast, reliable casting services that can reach our kilns on the same day you order.
Ethically sourced materials
Our precious metals and casting materials are sustainably sourced for life.
Happy customers
You can hear from our happy customers that we're the number one casters.
Product range
Our products and services are tailored to complete the manufacturing process.

Got something for us to cast?
Start your order below or get in touch to discuss your jewellery casting needs.
Jewellery Casting Scotland have provided a fabulous service for us for may years now, not only a pleasure to do business with, but a fantastic team of people too – we have recommended them to many other jewellers! The best in the business by far!
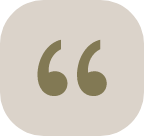
Linda Macdonald,
Linda Macdonald Jewellery
Our heartfelt thanks to Scotland Casting, not only for offering such expert casting of one of my husband’s jewellery designs, but also for taking over the finishing now that my husband sadly, is no longer with us. They made the whole process easy. They are a thoroughly professional company offering a great service, which has meant that my husband’s silver earring and pendant top design can continue to go out in the world.
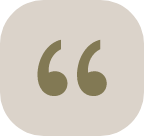
Honor & Sabrina,
Avalon Jewellery
Thank you for the photographs of our masters. What a good idea!
You are so organised and this idea works so well for us. The folders that you sent keep everything together and we can see what the codes represent when we have forgotten. Thank you.
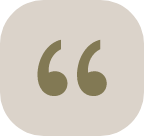
Sue Foster,
Aardvark Jewellery Ltd
We want to let you know that we think that you are doing a great job for us and we love the personal service. The urgent order for an 18ct red ring that you managed to get to us in time for our customer’s Wedding Day saved us red faces – thank you.
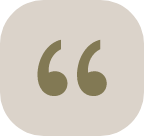
Nigel Blayney,
Cymru Gold
Within my over 20 year career in the jewellery business, I have worked with many casters but Jewellery Casting Scotland, who I have ordered my castings from for over a year is the one that I appreciate most for their quality and transparent pricing. In addition to that, the exceptionally easy communication and individual approach to every job means I don’t have to look any further for jewellery casting services in the future.
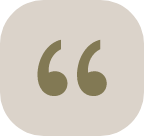
Wiktor,
Wiktor Jewellery
Traditional in our product but modern in its execution, the benefits of speaking with Mike and Trish about your casting needs are as important as the item itself. Fantastic people, fantastic knowledge and fantastic service!!
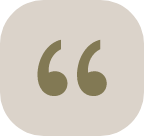
Alan Cathro,
The Iona Shop
Oh my! A great big thank you to all involved in casting my etched silver hares.
They arrived this morning and they are perfect. Delighted doesn’t even come close to describing how pleased I am.
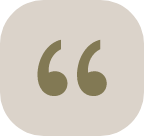
Jo Bignold,
Lucylou Designs
I have to let you know – I used to use Merrel Casting and another big caster in Birmingham, and I have never received such beautiful, smooth castings – thank you so much!
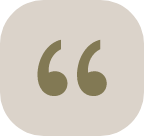