Preparing waxes and investing
No we've prepared the moulds we need to know how to make the waxes. Also, if you supply us with waxes, either carved or injected this is what we do with them.
...and now for the hard bit.
It may sound simple to squirt some wax into a mould but it's really extremely difficult to get a perfect reproduction. In the workshop we rate the crew on the vacuum wax injectors to be the most skillful people.
Vacuum Wax Injectors
Without a doubt, the bit of kits you need to fill a mould is a vacuum wax injector. This amazing device sucks the air out of the mould before shooting wax in under precisely controlled pressure. Many things can go wrong and it's very rare that the first injection is good enough for casting. All waxes are inspected under a lens for imperfections by our keen-eyed team.
Making trees ("Spruing up")
A wax pole is fixed inot a rubber base to form the trunk of the tree. The individual waxes on their sprue are melted into the trunk with precision to get the maximum number of waxes into a flask -anything from 1 to 300! If you have supplied a wax these join in with the rest of our production waxes which is why we can offer such keen pricing on low volumes.
Pouring Investment Plaster
The tree is now covered with a stainless steel cylinder, fitted into the rubber base. Investment plaster is now poured gently round the waxes under vacuum, eliminating pesky air bubbles. The mixer gives the flasks a "wee shoogle" to make sure the waxes have a nice tight fit. These are left now to stand for 2 hours, untouched. This is all done with extreme precision to get weights, volumes and temperatures correct. This is critical for consistent results in casting.
Burnout in the Kiln
The flasks are now gently placed in a kiln - up to about 20 in a load. The temperature is gently raised to melt out most of the wax and drive out the moisture from the plaster. Then slowly we raise the temperature of the flasks to 740°C and hold it there for 4 hours. This converts the basic investment plaster to a tough ceramic. We then cool it down to the desired casting temperature, ready for some molten metal.
...and that's the end of your waxes!

Jewellery Casting Scotland have provided a fabulous service for us for may years now, not only a pleasure to do business with, but a fantastic team of people too – we have recommended them to many other jewellers! The best in the business by far!
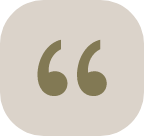
Linda Macdonald,
Linda Macdonald Jewellery
Our heartfelt thanks to Scotland Casting, not only for offering such expert casting of one of my husband’s jewellery designs, but also for taking over the finishing now that my husband sadly, is no longer with us. They made the whole process easy. They are a thoroughly professional company offering a great service, which has meant that my husband’s silver earring and pendant top design can continue to go out in the world.
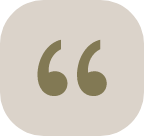
Honor & Sabrina,
Avalon Jewellery
Thank you for the photographs of our masters. What a good idea!
You are so organised and this idea works so well for us. The folders that you sent keep everything together and we can see what the codes represent when we have forgotten. Thank you.
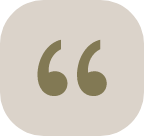
Sue Foster,
Aardvark Jewellery Ltd
We want to let you know that we think that you are doing a great job for us and we love the personal service. The urgent order for an 18ct red ring that you managed to get to us in time for our customer’s Wedding Day saved us red faces – thank you.
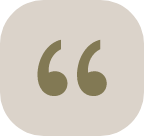
Nigel Blayney,
Cymru Gold
Within my over 20 year career in the jewellery business, I have worked with many casters but Jewellery Casting Scotland, who I have ordered my castings from for over a year is the one that I appreciate most for their quality and transparent pricing. In addition to that, the exceptionally easy communication and individual approach to every job means I don’t have to look any further for jewellery casting services in the future.
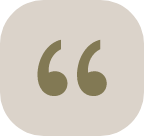
Wiktor,
Wiktor Jewellery
Traditional in our product but modern in its execution, the benefits of speaking with Mike and Trish about your casting needs are as important as the item itself. Fantastic people, fantastic knowledge and fantastic service!!
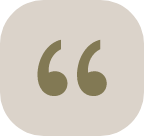
Alan Cathro,
The Iona Shop
Oh my! A great big thank you to all involved in casting my etched silver hares.
They arrived this morning and they are perfect. Delighted doesn’t even come close to describing how pleased I am.
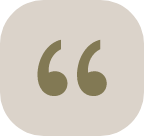
Jo Bignold,
Lucylou Designs
I have to let you know – I used to use Merrel Casting and another big caster in Birmingham, and I have never received such beautiful, smooth castings – thank you so much!
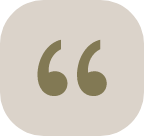
Nikki,
Eltikki Bespoke Jewellery
Got something for us to cast?
Start your order below or get in touch to discuss your jewellery casting needs.